
전기 전도성 접착제를 활용한 슁글드 스트링 상호연결을 위한 연구
© 2025 by the New & Renewable Energy
This is an Open Access article distributed under the terms of the Creative Commons Attribution Non-Commercial License (http://creativecommons.org/licenses/by-nc/3.0) which permits unrestricted non-commercial use, distribution, and reproduction in any medium, provided the original work is properly cited.
Abstract
The installation of solar power is increasing globally due to the strengthening of renewable energy transition policies, while initiatives like RE100 are accelerating sustainability in the domestic market. In the manufacturing process of solar modules, soldering metal ribbons to the busbars of solar cells is an essential step. However, the high-temperature soldering method poses risks of cell damage due to differences in thermal expansion coefficients and stress caused by heat. These issues are particularly pronounced when soldering metal ribbons to half-cut solar cells at both ends to connect shingled strings, as the process may lead to string warping. This study proposes a method to address these challenges by using electrically conductive adhesives (ECA) to bond metal ribbons. Experimental results demonstrate that stable metal ribbon connections can be achieved even at a reduced temperature of 150°C, compared to the conventional high-temperature process at 350°C, with an efficiency loss of approximately 1.325%. These findings indicate that ECA-based bonding methods offer an effective alternative for the manufacturing of shingled solar modules.
Keywords:
PV module, Shingled module, Electrically conductive adhesive, Low-temperature process, Metal ribbon키워드:
태양광 모듈, 슁글드 모듈, 전기 전도성 접착제, 저온 공정, 금속 리본1. 서 론
최근 여러 국가에서 친환경 에너지 전환 정책이 강하게 작용하면서 글로벌 태양광 설치용량이 늘어나고, 국내에서도 RE100과 같은 정책이 기업들의 친환경 전환을 지원하면서 새로운 성장 가능성이 열리고 있는 추세이다.[1,2] 태양광 모듈 제작 과정에서, 일반 태양광 모듈의 경우 풀사이즈 태양전지의 전극에 금속 리본을 솔더링하고, 이 솔더링된 리본들을 이어 하나의 스트링으로 구성한다. 또한, 슁글드 모듈의 경우 레이저로 분할된 분할 태양전지를 전기 전도성 접착제를 이용하여 긴 스트링으로 제작한 뒤, 이 스트링들을 직렬 또는 병렬로 연결하여 태양광 모듈로 제작한다.[3,4] Fig. 1에 나타낸 바와 같이, 스트링들을 연결하기 위해 스트링 끝 단 분할 셀의 버스바(Busbar)와 버스 리본(Bus Ribbon)은 일반 모듈과 같이 솔더링을 통해 전기적으로 연결된다.[5~8]
그러나 이 과정에서 열팽창 계수가 서로 다른 태양전지와 금속 리본은 기존 고온 솔더링이 진행한 후, 상온에서 냉각되는 과정에서 수측 응력이 발생하여 태양전지 또는 슁글드 스트링이 휘거나 파손될 위험성이 있다. 또한, 고온으로 인해 셀에 가해지는 열에의한 전기적 특성의 저하도 발생할 수 있다.[9] 특히 슁글드 모듈의 경우, 셀이 휘어짐에 따라 모듈의 내구성과 출력에 더 큰 영향을 미친다.
본 논문에서는 태양광 모듈 제작 시 사용되던 기존의 고온 솔더링 방식 대신, 저온에서도 태양전지 및 스트링 간의 상호 연결이 가능하도록 전기 전도성 접착제를 이용하였다. 그리고 기존의 고온 솔더링 방식과 전기 전도성 접착제를 이용한 금속 리본 접합 방식을 비교하였다. 비교 항목으로는 태양전지 휘어짐의 정도를 ANSYS Static Structural 내의 열 변형 해석을 통해 분석했으며, 전기적 특성도 함께 평가하였다. 이를 통해 슁글드 모듈 제작 과정에서 발생하는 스트링의 휘어짐 또는 파손을 개선하고, 태양광 모듈의 내구성과 성능을 향상 시키고자 하였다.
2. 실험 방법
본 논문에서는 기존 슁글드 스트링 제작에 사용되는 스트링거를 이용하여 금속 리본에 전기 전도성 접착제를 도포 하였으며, 전기 전도성 접착제로는 Henkel사의 Loctite ICP-8311을 사용하였다. Fig. 2와 같이 금속 리본에 전기 전도성 접착제를 도포 한 후 이를 셀의 버스바에 접합하였다. 스트링거에 내장된 핫플레이트(Hot Plate)의 온도와 시간에 따른 셀 및 금속 리본 접합 공정 최적화 조건을 확립하기 위해, 온도는 100°C에서 160°C 범위 내, 시간은 10초에서 40초 범위에서 전기 전도성 접착제 경화 테스트를 진행하였고, 금속 리본 연결 전후의 효율 저하율을 비교하였으며, EL 사진을 통해 금속 리본과 스트링이 전기적으로 잘 연결이 되었는지 확인하였다.
또한, 기존 고온 솔더링 방식과 본 논문에서 제시한 전기 전도성 접착제를 이용한 접합 방식을 비교하기 위해, 각각의 방식으로 금속 리본을 연결한 후 셀의 열변형을 분석하였다. 열 해석은 ANSYS에서 제공하는 유한 요소 해석 도구인 Static Structural Model을 사용하여 태양전지와 금속 리본의 사이 층의 물성을 전기 전도성 접착제 또는 솔더(Sn-Pb합금)를 적용하였을 때, 온도 변화에 따른 응력과 변형을 분석하였다. 이후 두 가지의 금속 리본 연결 방식에 따른 전기적 특성 차이만을 비교하기 위해 기존 고온 솔더링 방식과 전기 전도성 접착제를 이용한 금속 리본 접합 방식으로 각각 샘플을 제작하였다. 다른 환경 조건을 최소화 하기 위하여 풀 사이즈 태양전지의 버스바를 이용하여 샘플을 제작하여 측정 지그와 솔라 시뮬레이터를 이용하여 리본 연결 후 셀 및 스트링의 전기적 특성을 분석하였다.
3. 결과 및 고찰
3.1 전기 전도성 접착제를 이용한 금속 리본 접합 공정조건 확보
전기 전도성 접착제는 경화 온도와 시간에 따른 경화 정도의 차이로 접합 상태에 영향을 미치며, 이는 전기적 출력 특성의 차이로 나타난다. 이를 기반으로 최적의 접합 조건을 선정하기 위해 다양한 경화 온도와 시간에서 접합 테스트를 진행하였다.
전기 전도성 접착제를 도포 한 후 금속 리본을 접합하고, 온도나 시간이 부족하거나 과도한 조건에서 경화시키면 접합 강도가 일정 수준 이하로 떨어져 Fig. 3과 같이 금속 리본의 박리가 발생하였다. 실험을 통해 박리 없이 금속 리본이 완전히 접합된 조건과 그렇지 않은 조건을 구분하였으며, 금속 리본 부착 면이 태양전지의 전면 또는 후면인 경우를 나누어 Table 1과 Table 2에 정리하였다.
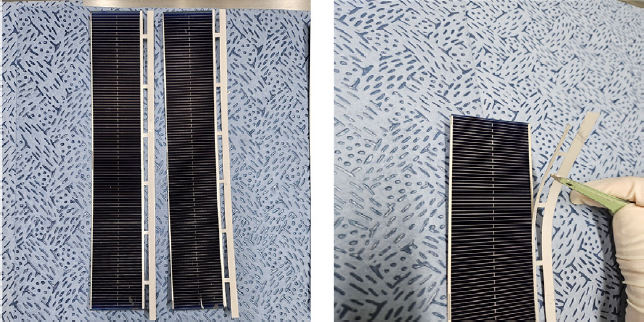
(Left) Well-bonded metal ribbon under optimal curing conditions and (Right) Metal ribbon delamination under suboptimal conditions
접합 테스트 결과, 금속 리본을 태양전지 전·후면에 접합하려면 최소 150°C 이상에서 20초 이상의 경화가 최소 공정 조건이다. 따라서 각 조건에서 슁글드 2 접합 셀에 금속 리본 접합 후 EL 측정을 진행함으로써 전기적으로 잘 연결되었는지 확인하였으며, 결과는 Fig. 4에 나타나 있다. (b) 조건에서 접합한 샘플은 접합 상단부에 결함이 발생해 어둡게 나타났다. 나머지 (a), (c) 조건의 경우 둘 다 기존 고온 솔더링 조건 (d) 샘플과 유사한 EL 특성을 보였으나 본 논문에서는 금속 리본을 접합하는 온도를 최소화함으로써 열에 의한 셀의 손상을 줄이기 위하여 경화온도 150°C, 경화시간 30초를 최적의 조건으로 선정하였다.
3.2 절 열-구조해석을 이용한 태양전지의 열 변형률 분석
기존의 고온 솔더링 방식과 전기 전도성 접착제를 이용한 저온 접합 방식에 의한 태양전지의 열 변형률을 비교하기 위해, 두 가지 조건을 적용하여 열변형 분석을 진행하였다. 전기 전도성 접착제를 이용한 금속 리본 접합 최적 조건인 경화 온도 150°C, 경화 시간 30초 조건을 열변형 분석의 경계조건으로 적용하였고 솔더링 온도의 350°C를 적용하였다.
기존 고온 솔더링 방식과 본 논문에서 제안한 전기 전도성 접착제를 활용한 방식으로 발생하는 태양전지의 열 변형 분포는 각각 Fig. 5의 (a)와 (b)와 같이 나타났다. 최대 변형률을 나타낸 Table 3에 따르면, 기존 방식으로 350°C의 온도에서 금속 리본을 솔더링한 경우 태양전지의 최대 변형률은 1.553 mm로 나타났다. 반면, 전기 전도성 접착제를 도포한 후 150°C에서 경화하여 금속 리본을 접합하는 경우, 최대 변형률은 0.606 mm이다. 이는 본 논문에서 제안한 방식이 셀과 금속 리본의 상이한 열팽창 계수 차이로 인해 발생하는 휘어짐을 약 60.9% 감소시킬 수 있음을 의미한다.
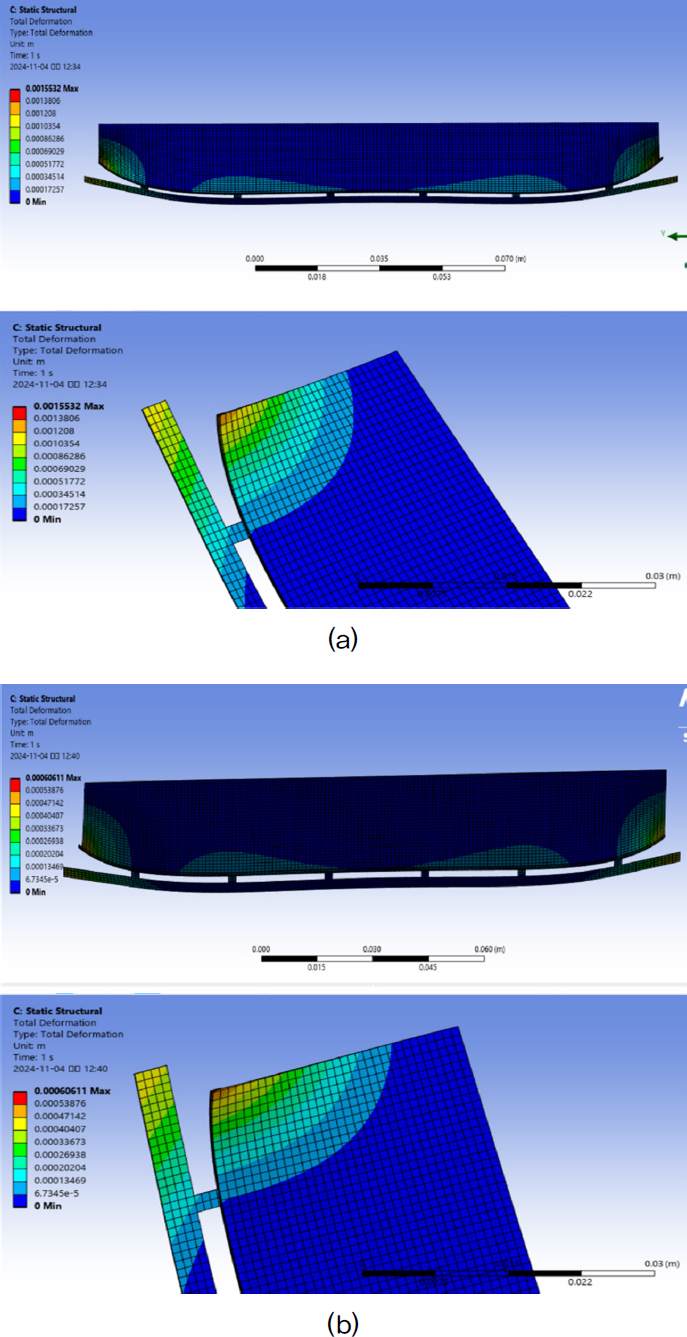
Comparison of solar cell deformation rates due to (a) High-temperature soldering and (b) ECA bonding
3.3 고온 솔더링 방식과의 출력 손실 비교
기존의 고온 솔더링 방식과 본 논문에서 제시한 전기 전도성 접착제를 이용한 접합 방식에 의한 태양전지의 효율 손실률을 비교하기 위해, 금속 리본 접합 전후의 효율 특성을 측정하였다. 리본에 의한 효율 저하율을 분석하기 위해서 측정의 경우 풀 사이즈 태양전지의 버스바에 금속 리본을 접합하는 방식으로 이외의 발생할 수 있는 다른 변수를 최소화하였으며, 동일한 측정 지그를 이용하여 금속 리본 전/후의 효율 측정을 함으로써 비교하였다. 결과는 Table 4에 제시되어 있다. Fig. 6에서 확인할 수 있듯이, 전기 전도성 접착제를 이용한 금속 리본 접합 방식으로 연결함에 따라 발생하는 평균 효율 손실률은 1.414%로 계산되었으며, 이는 기존 고온 솔더링 방식에 의한 평균 효율 손실률 1.999%와 비교할 때 유사한 값을 가짐을 알 수 있었다.
4. 결 론
기존의 고온 솔더링 방식을 이용하여 금속 리본을 연결 할 경우, 고온에서 접합된 부위가 열에 의해 변형되거나 손상되는 현상이 발생할 수 있으며, 이로 인해 전기적 특성에 영향을 미치거나 큰 열변형으로 인해 파손될 위험이 존재한다. 반면, 본 논문에서 제안한 전기 전도성 접착제를 이용한 솔더링 방식은 기존의 약 350°C에서 진행되는 고온 솔더링과 달리, 150°C라는 저온에서 유사한 전기적 특성을 유지하면서 금속 리본을 연결할 수 있도록 하였다. 태양전지와 금속 리본의 열팽창 또는 수축량 차이로 인해 발생하는 열변형률 분석 결과 단순히 온도를 낮춤으로써 열에 의한 변화율이 감소할 뿐만 아니라, 전기 전도성 접착제가 완충 층 역할을 하여 최종적으로 태양전지의 변형을 약 60.9% 감소시킬 수 있다는 것을 확인하였으며, 이를 통해 스트링 연결 시 발생할 수 있는 셀의 휨 현상 및 파손 위험을 줄일 수 있을 것으로 보인다. 이러한 결과는 슁글드 모듈 제작 과정에서 스트링 양 끝단 금속 리본 연결 시 발생할 수 있는 스트링 파손 위험을 감소시키는 데 기여할 수 있으며, 고출력 슁글드 모듈 제조에 중요한 역할을 할 것으로 기대된다.
Nomenclature
EL : | Electroluminescence |
Subscript
RE100 : | Renewable Electricity 100% |
Acknowledgments
본 논문은 2023년도 정부(산업통상자원부)의 재원으로 한국에너지기술평가원의 지원을 받아 수행된 연구 입니다(20213030010290, 장기 신뢰성(25년 이상)과 안정성이 확보된 건물형 태양광 핵심 소재 개발). 본 연구는 2023년도 산업통상자원부의 재원으로 한국에너지기술평가원(KETEP)의 지원을 받아 수행한 연구 과제입니다(RS-2023-00266248).
References
- Chae, Y., Moon, T., Kim, D., Lee, D., Jung, S., and Lee, K., 2016, “Development of a system dynamics model to strengthen the capacity to respond to climate change”, Korea Institute for Environmental Policy and Evaluation (KEI), https://scienceon.kisti.re.kr/commons/util/originalView.do?cn=TRKO201800014460&dbt=TRKO&rn=, .
- Kang, H., 2023, “Green innopark industrial complex 4.0 basic plan for carbon neutrality and RE100”, KRIHS Issue Report, 80, https://www.krihs.re.kr/gallery.es?mid=a10103080000&act=view&bid=0024&list_no=30053, .
-
Rehman, S., Bader, M.A., and Al-Moallem, S.A., 2007, “Cost of solar energy generated using PV panels”, Renew. Sustain. Energy Rev., 11(8), 1843-1857.
[https://doi.org/10.1016/j.rser.2006.03.005]
-
Vinod, Kumar, R., and Singh, S.K., 2018, “Solar photovoltaic modeling and simulation: As a renewable energy solution”, Energy Reports, 4, 701-712.
[https://doi.org/10.1016/j.egyr.2018.09.008]
-
Mittag, M., Zech, T., Wiese, M., Blasi, D., Ebert, M., and Wirth, H., 2017, “Cell-to-Module (CTM) analysis for photovoltaic modules with shingled solar cells”, Proc. 2017 IEEE 44th Photovoltaic Specialist Conference (PVSC), 1531-1536.
[https://doi.org/10.1109/PVSC.2017.8366260]
-
Chowdhury, S., Cho, E.C., Cho, Y., Kim, Y., and Yi, J., 2020, “Analysis of cell to module loss factor for shingled PV module”, New. Renew. Energy, 16(3), 1-12.
[https://doi.org/10.7849/ksnre.2020.0009]
-
Theunissen, L., Willems, B., Burke, J., Tonini, D., Galiazzo, M., and Henckens, A., 2018, “Electrically conductive adhesives as cell interconnection material in shingled module technology”, Proc. AIP Conference, 1999(1), 080003.
[https://doi.org/10.1063/1.5049305]
- Jee, H., Moon, D., Song, J., and Jeong, C., 2018, “Shingled string for the high performance photovoltaic module”, Current Photovoltaic Research, 6(4), 119-123.
- Kim, J., Kim, J., Jeong, C., Choi, W., and Lee, J., 2021, “Study on shingled string interconnection for high power solar module”, J. Korean Inst. Electr. Electron. Mater. Eng., 34(6), 449-453.