
Degradation of Backsheets for Crystalline Photovoltaic Modules under Damp Heat Test
Copyright ⓒ2016 by the New & Renewable Energy
This is an Open Access article distributed under the terms of the Creative Commons Attribution Non-Commercial License (http://creativecommons.org/licenses/by-nc/3.0) which permits unrestricted non-commercial use, distribution, and reproduction in any medium, provided the original work is properly cited.
Abstract
The reliability of crystalline silicon photovoltaic (PV) modules is determined not only by the efficiency loss of the silicon cells but also by the degradation of other components (ethyl vinyl acetate, ribbon, glass, and backsheet). Among these components, the backsheet provides electrical insulation and physical support, and acts as a barrier against moisture and weathering of the PV module. We investigated the degradation of different types of backsheets under damp heat conditions [95°C/85% relative humidity (R.H), 85°C/85% R.H]. During the damp heat treatment, tensile tests were carried out to investigate the mechanical degradation of the backsheets. The molecular weight of the polyethylene terephthalate (PET) in the backsheets was measured by gel permeation chromatography (GPC) to understand the intrinsic mechanism of degradation. After damp heat test, mechanical degradation of backsheet occurred significantly beyond passing the specified molecular weight region of PET film in backsheet materials. By finding the correlation between tensile strength and the molecular weight of the backsheets, our results make it possible to improve the reliability of backsheets.
Keywords:
Backsheet, PET Degradation, Tensile strength, GPC, Molecular weight1. Introduction
As a promising renewable energy source, photo-voltaic (PV) energy is gaining great support and concern from scientists worldwide. As the efficiency of crystalline PV modules approaches the theoretical value, the development of a crystalline PV module is driven by the need to reduce cost and improve long-term reliability. The long-term reliability of a crystalline PV module can be achieved by under-standing the degradation mechanism of each component comprising a crystalline PV module.[1–3] Among those components, the glass and the polymeric backsheet protect the inner silicon cell of the PV module from external stresses such as an electric insulator.[4,5] In particular, the backsheet material is more vulnerable to the external environment than the glass because it is designed using multiple layers of polymeric materials[6] such as polyethylene terephthalate (PET), polyvinyl fluoride (PVF), and polyvinylidene fluoride (PVDF).[7,8] In these materials, PET is commonly used as the core material for all types of backsheets. PET has a high crystalline melting temperature (260°C), and the stiff polymer chains in PET impart high mechanical strength, toughness, and fatigue resistance up to 150–175°C, as well as good chemical resistance.[9]
In our study, damp heat tests were carried out to accelerate the field conditions for various types of backsheets with a PET core layer. Under damp heat conditions, we investigated the mechanical properties of the backsheet materials to determine their degree of degradation, and we analyzed the change of molecular weight to understand the intrinsic mechanism of degradation. Degradation is a chemical process that affects not only the chemical composition of the polymer but also the physical parameters such as mechanical properties, chain conformation, molecular weight, molecular weight distribution, and crystallinity.[10] Therefore, we reveal the correlation between the mechanical properties and the molecular weight of the backsheet materials, and suggest that this correlation is a key factor in improving the reliability of backsheet materials.
2. Experiment
Three different types of backsheets were prepared for this study. All the backsheets for our study were typical three-layer polymer laminates, as shown in Fig. 1.
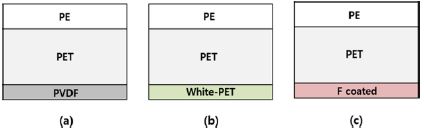
Three types of backsheets used in our experiment: (a) PVDF-laminated backsheet, (b) PET-laminated backsheet, and (c) fluorine-coated backsheet
Although the core layer of each backsheet was PET and the films on the cell side were all white polyethylene (PE) with TiO2 (titanium dioxide) pigment, the peripheral layers exposed directly to the harsh external environment were a polyvinylidene fluoride (PVDF)-laminated film, a PET-laminated film, and a fluorine-coated backsheet. PVDF films laminating method and fluorine-coating method have been adapted in order to reduce the module cost with high environment-resistance, instead of a polyvinyl fluoride (PVF) film (a type of fluoropolymer), which is widely used in outer layer of backsheets. We also investigate the effect of polyethylene terephthalate (PET) as peripheral layer of backsheet due to strong mechanical strength.[7,11]
The specimens 5 mm wide and 120 mm long were prepared for the tensile strength and damp heat tests. To investigate the effect of temperature, the samples were tested at 85°C and 95°C at a fixed relative humidity (R.H) of 85%. During the 85°C/85% R.H and 95°C/85% R.H damp heat tests, the tensile strength was measured every 250 h and 200 h. After 1200 h under 95°C/85% R.H, samples were broken during handling, allowing us to investigate the mechanical degradation behavior under 95°C/85% R.H condition. On the other hand, the tensile strength of the sample subjected to 85°C/85% R.H was measured over 2000 h due to the less harsh conditions. The tensile strength was measured as a function of the exposure time to investigate how well the material could maintain its initial performance. The tensile tests were conducted at a testing speed of 1 mm/s using a tensile testing system (MTS 858 Systems). After the tensile test, the fractures of each specimen were observed by optical microscope to find the crystallinity of the PET films as core materials.
The molecular weight of the PET layer in the backsheet was determined by gel permeation chromatography (GPC) analysis at 600, 1000, and 2000 h under 95°C/85% R.H conditions to identify the polymeric degradation of the PET layer.[12] The molecular weight of PET determines the tensile strength of the backsheet.[13] Analysis was performed on a Waters GPC System (Waters Corporation) and the signals were detected using Waters 410 differential refractometer detectors. Each sample (50 μL) was chromatographed in 1,1,1,3,3,3-hexafluoroisopropanol (HFIP) as the mobile phase with a 0.6 mL/min flow rate using TSKgel superAWM-H (6.0 × 150 mm) columns. The whole system, including columns, detectors, and interdetector tubing, was maintained at a constant temperature of 40°C. The molecular weight calibration line was established using polymethylmethacrylate (PMMA) as a reference sample. Number average molecular weights were calculated using Eq. (1) and they were normalized for comparison of the degradation rate.[14]
(1) |
where is the average molecular weight and Ni is the number of polymers with molecular weight Mi.
3. Results
Fig. 2(a) shows the initial tensile strengths of the three types of backsheet as force–displacement curves and Fig. 2(b) compares their maximum tensile strength. The maximum tensile strength of the PET-laminated backsheet is higher than that of the PVDF-laminated and fluorine-coated backsheets. The investigated unaged PET materials exhibited ductile behavior. PET elastic modulus values of approximately 4000 MPa.[7] In contrast, the PVF and PVDF fluoropolymers exhibited significantly lower elastic modulus values ranging from 1500 to approximately 2000 MPa.[7] Therefore, the elongation of the fluorine-coated and PVDF-laminated backsheet were larger than PET- laminated backsheet due to lower elastic modules.
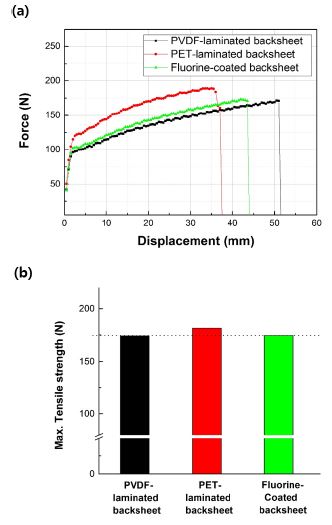
(a) Tensile strength of three types of backsheets as a function of displacement and (b) maximum tensile strength of unaged backsheets
Fig. 3 shows the change of tensile strength of the backsheet materials as a function of aging time for each test condition. In all specimens, the tensile strength of backsheet decreased slightly up to 2000h under the condition of 85°C/85% R.H, whereas the tensile strength decreased significantly after passing 600 h under the condition of 95°C/85% R.H. The tensile strength of the PET-laminated backsheet was higher than that of the others under both damp heat conditions. The PVDF-laminated backsheet degraded, followed by the fluorine-coated backsheet. PET-laminated backsheets contain hydrolysis-resistant PET, which maintains its performance integrity longer than regular PET. [15,16] The PVDF-laminated backsheet had more resistance against water vapor than the fluorine-coated backsheet. The decrease in mechanical strength is caused by the hydrolytic and thermal degradation of the organic materials in backsheet materials.
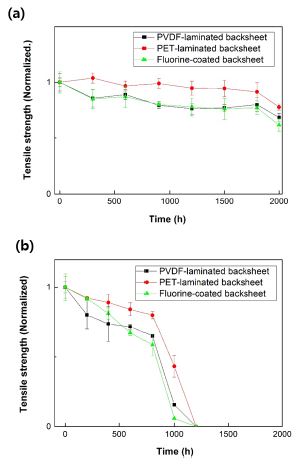
Variation of tensile strength for backsheet materials under (a) 85°C/85% R.H and (b) 95°C/85% R.H conditions
Moreover, it has been reported that the drop in tensile strength of PET materials is mostly due to hydrolysis of the PET polymer.[17-19] As shown in Fig. 3, the rate of hydrolytic degradation increased with increasing temperature.
To find out the hydrolysis mechanism of the PET polymer, we also observed optical micrographs of the cross sections of the backsheets subjected to 95 °C/85% R.H conditions for more than 1000 h after tensile testing. Fracture cracks were mainly found in the PET core material for all the backsheets, as shown in Fig. 4.
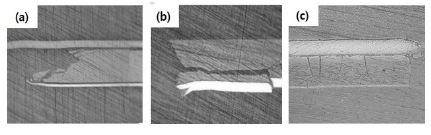
Cross-sectional optical micrographs of fracture of PET films after 1000 h under 95°C/85% R.H conditions for (a) PVDF-laminated backsheet, (b) PET-laminated backsheet, and (c) fluorine-coated backsheet
At the point of physical rupture of the specimens the PET films in the backsheet materials cracked, resulting in brittle fracture. This brittle fracture was caused by an increase of crystallization in the PET film during the application of damp heat. Cracking of the backsheet is potentially serious to electric safety. The fabrication of high-durability PET films is the one of the key factors to improving the long- term reliability of PV modules. The increase in crystallinity is caused by the generation of low- molecular-weight compounds.[20,21]
To clarify the degradation mechanism of the PET film of the backsheets, the molecular weight of the PET film was measured by using a GPC analyzer at specified time intervals under 95°C/85% R.H conditions. GPC, also known as size-exclusion chromatography (SEC), can obtain the molecular weight distribution of polymers. The molecular weight for all the unaged PET polymers was approximately 13,000. After being subjected to damp heat, it dramatically decreased to approximately 500 (Fig. 5). The degradation of PET polymers with different types of end-groups on the small polymer chain results in a decrease in the molecular weight through hydrolysis of the PET polymer.
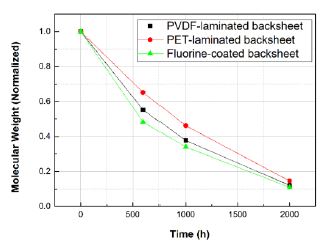
Variation of molecular weight (normalized) for the three types of backsheets under 95°C/85% R.H conditions
Significant hydrolysis of PET is known to occur in moist, wet, or humid conditions at temperatures above Tg. Hydrolysis of PET results in different types of end-groups on the polymer chain.[22] The initial step is the scission of the chain of the ester linkage, resulting in a decrease in molecular weight and an increase in number of carboxyl end-groups. The methylene group, which is located at the β position to the carbonyl group, is the main point where the decomposition process is initiated. The main side reaction is β scission of the ester linkage, resulting in a vinyl-terminated carboxylate unit and carboxyl-terminated units, as shown in Fig. 6. The formation of acetaldehyde is explained generally through the McLafferty rearrangement involving a six-membered transition state occurring through inter- or intra-molecular hydrogen shifts in the methylene group, which is located at the β position relative to the carbony l group.[9] The results include an increase in carboxylic and aldehyde end groups and an increase in smaller chain fragments (Fig. 6). Researchers have reported density changes during the degradation process,[22] which have been attributed to the crystallization process. Crystallinity changes occurring during degradation are extremely important because the morphology governs things such as small molecule transport and tensile strength. It has also been found by researchers that the initial degree of crystallinity greatly affects the rate of hydrolysis.[23,24]
The molecular weight of a polymer is one of the key parameters determining its physical properties such as stiffness, strength, and toughness.[25-27] The GPC results showed that during the application of damp heat, the molecular weight of the PET films decreased in all specimens, matching well with the decrease in tensile strength, as shown in Fig. 3. It is known that the relation between tensile strength and the molecular weight of a polymer can be approximated by a proportional relation.[28,29]
Equation (2) shows that the tensile strength (S)molecular weight (M) relation for a polymer can be approximately presented by the inverse relation.[19,30]
(2) |
A decrease of tensile strength of backsheet materials can be plotted as a function of the molecular weight of the PET film over a specific time, as shown in Fig. 7. The tensile strength of the backsheet materials did not change considerably with decreasing molecular weight of the PET film to 8000. However, in the range of 6000-8000 molecular weight), the tensile strength of the backsheet materials decreases sharply as compared to the slight reduction of the molecular weight of the PET film. Using Fig. 7, we could predict that properties of the degraded backsheets such as tensile strength and crystallinity from the molecular weight of PET by GPC analysis. In other words, during application of damp heat, the mechanical durability of backsheet materials can be retained before the molecular weight of the PET film decreases to the transient-molecular-weight region.
4. Conclusions
We demonstrated the degradation of backsheet materials by investigating the tensile strength and molecular weight. The tensile strength of backsheet materials decreased during the damp heat test (95 °C/85% R.H, 85°C/85% R.H), although the PET filmlaminated backsheet was superior to the others. This result shows that the PET film, which formed the core layer in the backsheet materials, degraded and became brittle due to the increased crystallinity of the PET polymer during the application of damp heat. After the damp heat test, the brittle fracture of the core PET film was revealed microscopically, and we showed photographs of the internal cracks of the PET film. By analyzing the molecular weight of the PET film, the decrease of the molecular weight of the PET film was correlated with the tensile strength of the backsheet materials.
In addition, and regardless of the backsheet material, it was found that significant mechanical degradation of the backsheet occurred once the molecular weight of the PET film decreased below a specified region. Based on our results, we can establish the prognosis of backsheet materials by finding the degradation factor of backsheet materials for assuring the long-term reliability of backsheet materials.
Acknowledgments
This work was supported by the New & Renewable Energy Program of the Korea Institute of Energy Technology Evaluation and Planning (KETEP) grant funded by the Korea Government Ministry of Knowledge Economy (20133030011150).
References
- D. L. King, M. A. Quintana, J. A. Kratochvil, D. E. Ellibee, and B. R. Hansen, (2000), “Photovoltaic Module Performance and Durability Following Long-Term Field Exposure”, Prog. Photovoltaics, 241.
-
I. V. Fisher, K. D Dobson, J. Nair, E. Bezalel, G. Hodes, and D. Cahen, (2003), “Factors affecting the stability of CdTe/CdS solar cells deduced from stress tests at elevated temperature”, Adv. Funct. Mater, 13, 289.
[https://doi.org/10.1002/adfm.200304259]
- M. A. Cluintana, D. L. King, T. J. McMahon, C. R. Osterwald, (2002), “Commonly observed degradation in field-aged photovoltaic modules”, Photovoltaic Specialists Conference (PVSC), 29th IEEE1436.
-
D. Wu, J. Zhu, T. R. Betts, and R. Gottschalg, (2000), “Degradation of interfacial adhesion strength within photovoltaic mini-modules during damp-heat exposure”, Prog. Photovoltaics, 22, p796-809.
[https://doi.org/10.1002/pip.2460]
- W. Gambogi, S. Kurian, B. Hamzavytehrany, A. Bradley, and J. Trout, (2011), “The Role of Backsheet in Photovoltaic Module Performance and Durability”, 26th European Photovoltaic Solar Energy Conference and Exhibition (PVSEC), p3325-3328.
-
Y. Zhang, J. Xu, J. Mao, J. Tao, H. Shen, Y. Chen, Z. Feng, P. J. Verlinden, P. Yang, and J. Chu, (2015), “Long-term reliability of silicon wafer-based traditional backsheet modules and double glass modules”, RSC Adv, 5, p65768-65774.
[https://doi.org/10.1039/C5RA11224A]
-
G. Oreski, and G. M. Wallner, (2005), “Aging mechanisms of polymeric films for PV encapsulation”, Sol. Energy Mater. Sol. Cells, 79, p612-617.
[https://doi.org/10.1016/j.solener.2005.02.008]
- K. J. Geretschlager, G. M. Wallner, and J. Fischer, (2015), “Raman and Infrared Microscopical Analysis of Multilayer Backsheets”, 26th EU Photovoltaic Solar Energy Conference and Exhibition (PVSEC), p3499-3502.
- S. Venkatachalam, S. G. Nayak, J. V. Labde, P. R. Gharal, K. Rao, and A. K. Kelkar, (2012), “Degradation and Recyclability of Poly (Ethylene Terephthalate)”, Polyester, H. M. Saleh, InTech, Croatia, Chap. 4, p75-98.
-
E. Wanga, H. E. Yang, J. Yen, S. Chi, and C. Wang, (2013), “Failure Modes Evaluation of PV Module via Materials Degradation Approach”, Energy Procedia, 33, p256-264.
[https://doi.org/10.1016/j.egypro.2013.05.066]
-
G. Oreski, and G. M. Wallner, (2005), “Delamination behaviour of multi-layer films for PV encapsulation”, Sol. Energy Mater. Sol. Cells, 89, p139-151.
[https://doi.org/10.1016/j.solmat.2005.02.009]
-
J. C. Moore, (1964), “Gel permeation chromatography. I. A new method for molecular weight distribution of high polymers”, J. Polym. Sci, 2, p835-843.
[https://doi.org/10.1002/pol.1964.100020220]
-
P. Sánchez-Friera, M. Piliougine, J. Peláez, and J. Carretero, (2011), “Analysis of degradation mechanisms of crystalline silicon PV modules after 12 years of operation in Southern Europe”, Prog. Photovoltaics, 19, 658.
[https://doi.org/10.1002/pip.1083]
-
A. E. Hamielec, and A. C. Ouano, (1978), “Generalized Universal Molecular Weight Calibration Parameter in GPC”, J. Liq. Chromatogr, 1, p111-120.
[https://doi.org/10.1080/01483917808068382]
- G. D. Barber, G. J. Jorgensen, K. Terwilliger, S. H. Glick, J. Pern, and T. J. McMahon, (2002), Photovoltaic Specialists Conf, (2002), “New Barrier Coating Materials for PV Module Backsheets”, 29th IEEEp1541-1544.
- P. Hülsmann, C. Peike, M. Blüml, P. Schmid, K. Weiß, and M. Köhl, (2012), “Impact of Permeation Properties and Backsheet-Encapsulant Interactions on the Reliability of PV Modules “, IMECE, 4, 5.
-
M.D. Kempe, (2006), “Modeling of rates of moisture ingress into photovoltaic modules”, Sol. Energy Mater. Sol. Cells, 90, p2720-2738.
[https://doi.org/10.1016/j.solmat.2006.04.002]
-
M. A. Hallam, G. Pollard, and I. M. Ward, (1987), “Relationship between tensile strength and molecular weight of highly drawn polyethylenes”, J. Mater. Sci, 6, p975-976.
[https://doi.org/10.1007/bf01729888]
-
Smith P., P. J. Lemstra, and J. P. Pijpers, (1982), “Tensile strength of highly oriented polyethylene. II. Effect of molecular weight distribution”, J. Polym. Sci. Polym. Phys. Ed., 20, p2229-2241.
[https://doi.org/10.1002/pol.1982.180201206]
-
F. D. Novoa, D. C. Miller, and R. H. Dauskardt, (2014), “Environmental mechanisms of debonding in photovoltaic backsheets”, Sol. Energy Mater. Sol. Cells, 120, p87-93.
[https://doi.org/10.1016/j.solmat.2013.08.020]
- A. Iguchi, H. Hirabayashi, T. Hayashi, K. Yamada, and H. Nishimura, (2014), “Evaluation of Degradation of PET Film by Partial Discharge Method”, Mater. Sci. Appl, 5, p33-38.
-
C. Sammon, J. Yarwood, and N. Everall, (2000), “An FT-IR study of the effect of hydrolytic degradation on the structure of thin PET flms”, Polym. Degrad. Stab, 67, p149-158.
[https://doi.org/10.1016/S0141-3910(99)00104-4]
-
M. Edge, M. Hayes, M. Mohammadian, N. S. Allen, T. S. Jewitt, K. Brems, and K. Jones, (1991), “Aspects of poly (ethylene terephthalate) degradation for archival life and environmental degradation”, Polym. Degrad. Stab, 32, p131-153.
[https://doi.org/10.1016/0141-3910(91)90047-U]
-
R. C. Golike, and S. W. Lasoski, (1960), “Kinetics of hydrolysis of polyethylene terephtalate films”, J. Phys. Chem, 64, p895-898.
[https://doi.org/10.1021/j100836a018]
-
E. Pirzadeh, A. Zadhoush, M. Haghighat, (2007), Hydrolytic and Thermal Degradation of PET Fibers and PET Granule: The Effects of Crystallization, Temperature, and Humidity”, J. Appl. Polym. Sci, 106, p1544-1549.
[https://doi.org/10.1002/app.26788]
- W. McMahon, and C. T. Camilli, (1959), “Physical properties evaluation of compounds and materials_Degradation Studies of Polyethylene Terephthalate”, J. Chem. Eng, 4, p57-79.
-
L. J. Fetters, D. J. Lohse, D. Richter, T. A. Witten, and A. Zirkel, (1994), “Connection between Polymer Molecular Weight, Density, Chain Dimensions, and Melt Viscoelastic Properties”, Macromolecules, 27, p4639-4647.
[https://doi.org/10.1021/ma00095a001]
-
D. F. Farrar, R. K. Gillson, (2002), “Hydrolytic degradation of polyglyconate B: the relationship between degradation time, strength and molecular weight”, Biomaterials, 23, p3905-3912.
[https://doi.org/10.1016/S0142-9612(02)00140-0]
-
P. J. Flory, (1945), “Tensile Strength in Relation to Molecular Weight of High Polymers”, J. Am. Chem. Soc, 67, p2048-2050.
[https://doi.org/10.1021/ja01227a506]
-
N. Kim, H. Kang, K. Hwang, C. Han, W. Hong, D. Kim, E. Lyu, and H. Kim, (2014), “Study on the degradation of different types of backsheets used in PV module under accelerated conditions”, Sol. Energy Mater. Sol. Cells, 120, p543-548.
[https://doi.org/10.1016/j.solmat.2013.09.036]